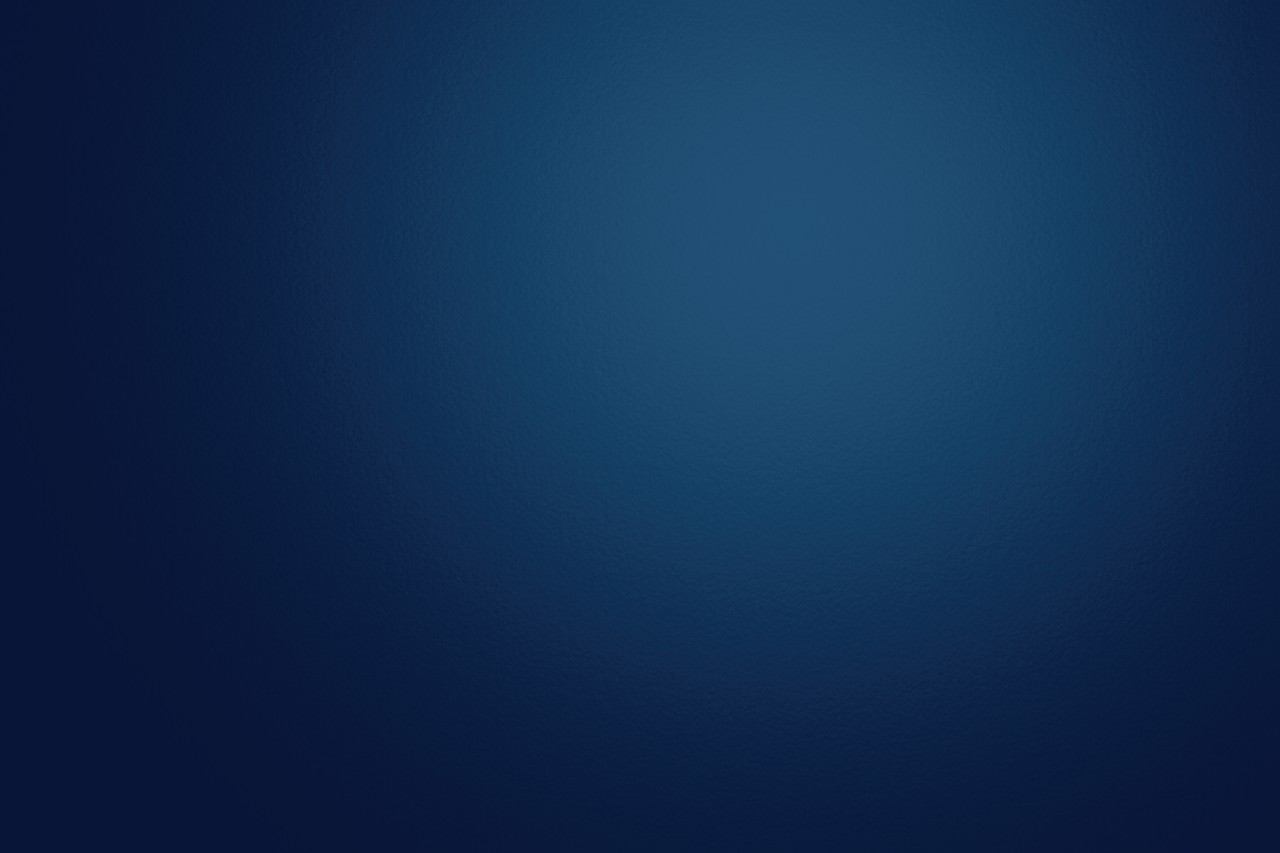
Kander Research
302A Lawrence N. Fields
DEC Center
Philadelphia, PA 19144
Contact
The increasing global demand for sustainable and environmentally friendly materials has driven significant research into bio-based polymers and fibers. This comprehensive research project aims to explore and develop innovative solutions utilizing agricultural by-products, specifically focusing on hemp and cotton. Our key initiatives include the synthesis of Hemp-Derived Cellulose Nanoparticles (CNPs), production of Poly-3-Hydroxybutyrate (P3HB) from both hemp and cotton sources, and the testing and optimization of hemp fiber properties. Additionally, we are investigating the efficacy of water retting processes for hemp stalks, the development of polypropylene/polylactic acid (PP/PLA) blends, and the extraction of valuable compounds using Supercritical Fluid (SCF) CO2 techniques. By leveraging these diverse yet interconnected projects, we aim to advance the field of sustainable materials and contribute to the development of high-performance, eco-friendly products.
Research Projects
Enhanced Properties of Polypropylene-Polylactic Acid Blends via Cryogenic Mechanical Alloying: Processing and Characterization
This project focuses on the development and characterization of polypropylene (PP) and polylactic acid (PLA) polymer blends using cryogenic mechanical alloying (CMA), a technique traditionally used for metals and ceramics but novel for polymers. PLA, a biodegradable polymer derived from renewable resources, is combined with PP, a versatile petroleum-based polymer, to enhance the properties of both. The primary aim is to overcome PLA's limitations, such as brittleness and low heat deflection temperature, by leveraging PP's superior mechanical and thermal properties. PP and PLA successfully blended without chemical compatibilizers using CMA, leading to potentially unique morphologies and improved crystallization kinetics. The films formed from these blends have been subjected to rapid compression molding to minimize phase segregation, followed by detailed thermal and morphological analyses using differential scanning calorimetry (DSC) and polarized light microscopy. Additionally, the mechanical properties of the films have been evaluated through dynamic mechanical analysis (DMA), and their suitability for packaging applications. As we approach the completion of this project, our future steps involve finalizing the analysis of dyed PLA powders blended with PP and publishing our findings to contribute to the advancement of biodegradable polymer composites.
Synthesis & Characterization of P3HB Biopolymer Manufactured from Waste Biomass
This project looks to utilize waste biomass sugars as a feedstock for bacterial fermentation to create a poly-3-hydroxybutyrate in a scalable, economically feasible manner. Poly-3-hydroxybutyrate (P3HB) is a biopolyester that is naturally produced intracellularly by certain bacteria, such as Ralstonia Eutropha, as a means of energy storage in stressed environments. P3HB has existed in the market before but fallen out; P3HB’s high costs must be reduced to compete as a biodegradable alternative to common petrol-based thermoplastics. Currently, the team is working with Cotton Incorporated, experimenting with cotton-derived glucose as a carbon source in the fermentation process. Thus far, P3HB has been successfully created using the cotton-derived glucose and commercial glucose on a benchtop scale: with fermentation of 100mL in shake flasks and polymer extraction using chloroform and evaporation. The team has also begun the process of transitioning our upstream bioprocess into a 2L stirred tank bioreactor as a way to mimic large scale production. The growth conditions of the bacteria directly influence the final polymer yield and characteristics; thus it is important we explore different methods of production and extraction at this stage. The future work of this team entails these tests, varying specific growth conditions for optimization in P3HB production, as well as thermal and mechanical testing for characterization. In addition to this, the team plans to create a hemp-derived glucose source using a supercritical CO2 extractor, which may provide an even cheaper raw material, thus a more affordable product.
Developing a Hemp Fiber Testing Method
With a recent increased interest in the industrial hemp sector, there is a new need for efforts towards the standardization of testing procedures to help the industrial hemp economy flourish in the upcoming years. Our efforts are a contribution to develop a fiber bundle testing protocol for hemp fiber.
Since hemp fibers have higher mechanical strength compared to other conventional fibers, we are trying to develop a new test method using a microtester to test the unique mechanical properties. 64 Hemp fiber samples were provided to our group by the Rodale Institution. Our goal is to develop a testing method in hopes to contribute information towards the industry.
This team has developed a test method that uses a microtester with special designed grips to hold fibers in place. Each specimen used in trials was weighed and measured before mechanical testing. Different gauge lengths were also considered to interpret results. The microtester pulls the fibers until break and records all mechanical data.
In the future the team is planning to use the collected data to work with the Rodale Institute to see how growing conditions affect the mechanical properties. Plots given to us by Rodale had different soil and environmental conditions.
Manufacture & Characterization of Hemp-Derived Cellulose Nano-nano Crystals in Polymer Matrices
This project focuses on developing sustainable, biodegradable composite materials by integrating cellulose nanocrystals (CNCs) and cellulose microcrystals (CMCs) derived from hemp fibers with different biodegradable polymers. The bast fiber of hemp has been transformed into CNCs and CMCs using optimized laboratory processes. Hydrolysis with three types of acids, including replacing organic acids like citric acid with sulfuric acid, was performed on hemp fiber to create a more sustainable hydrolysis process and evaluate their effectiveness. The reaction time for citric acid hydrolysis was varied to examine changes in particle morphology, quality, and yield, and citric acid was recovered and assessed for quality. Composite fabrication involved making PVA cast films with CNCs in solution and pressed PLA films with CMCs cryo-milled into powdered polymer. Characterization techniques such as tensile tests, FTIR analysis, TGA, DSC, and microscopy were used to evaluate mechanical behavior, chemical structure, thermal properties, and morphology. Future steps involve using a hemp-derived biopolymer to create a fully hemp-based composite material, enhancing the economic viability and scalability of the hemp supply chain. This includes using techniques like Dynamic Light Scattering (DLS) for further analysis and zeta potential measurements for surface charge characterization, as well as modifying cellulose nanoparticle surfaces to improve biocompatibility for biomedical applications. The results will be disseminated through peer-reviewed publications and presentations to maximize impact and encourage the use of hemp in industrial applications.
Mechanizing the Water Retting Process of Hemp Stalks
Water retting is a very effective method of removing the fiber from hemp stalks. These fibers can then be applied to multiple different textile applications. However, water retting has been outlawed under new environmental protection acts because of its eutrophication of local waterways. A closed-loop mechanized process for water retting would be ideal because it allows for controlled conditions for the highest quality of fibers from the hemp stalks and prevents contaminated water from entering the waterways. A lab model was built for the project's first phase that would allow multiple conditions to be tested in a controlled environment to determine what conditions produce the best quality fibers. Since the lab model is a closed-loop system the growth of bacteria is a concern, stand still retting trials were conducted to see what chemical agents best controlled the formation of molds. Now that the lab model has been assembled the focus of the project is shifting to testing what conditions produce the best quality fibers in textile applications.